Download Our Brochure
Safety & Environmental Associates, Inc.
Safety Compliance, Environmental Reporting and Consulting, Industrial Hygiene and Training Programs in Arkansas, South Carolina, North Carolina and surrounding areas
Safety Compliance Services
SEA Inc. has a team of Safety professionals that are dedicated to ensuring compliance for customers in general industry, construction, and government agencies in Arkansas, South Carolina. North Carolina and surrounding areas.
Industrial Hygiene Services
SEA Inc. is a leading provider of industrial hygiene services in Arkansas, South Carolina and North Carolina that are designed to help businesses maintain a safe and healthy work environment for their employees.
Environmental Reporting & Consulting
Safety & Environmental Associates, Inc. provides environmental reporting and consulting services that help businesses stay compliant with environmental regulations and improve their sustainability efforts in Arkansas, South Carolina, North Carolina & surrounding areas.
Our Training Program
Training courses are customized to your site-specific needs – rather than a canned computer or video information-training course! Providing thorough training and ongoing support to employees minimizes environmental, health and safety risks by equipping them with the knowledge to work competently in every situation.
Construction Division
Contact us today to learn more about how our Construction Division can elevate the safety and efficiency of your construction projects in Arkansas, South Carolina and North Carolina. Together, we'll create a secure and successful construction environment that sets new industry standards.
Our Management Team:
SEA’s approach to project management is a team effort. Team members lend their individual experience and talents to each project insuring that all compliance issues are effectively managed and reflected for complete regulatory compliance. Each project is evaluated to determine the scope of work and to match team resources with specific needs of the client.
Our Community Events:
SEA Inc. takes immense pride in its active involvement in community events, reflecting their commitment to giving back and strengthening local ties. Whether through sponsorships, volunteer work, or organizing charitable initiatives, SEA Inc. demonstrates a strong dedication to supporting the well-being and vibrancy of the communities they serve. Click below to view our community involvement.
OUR BLOGS
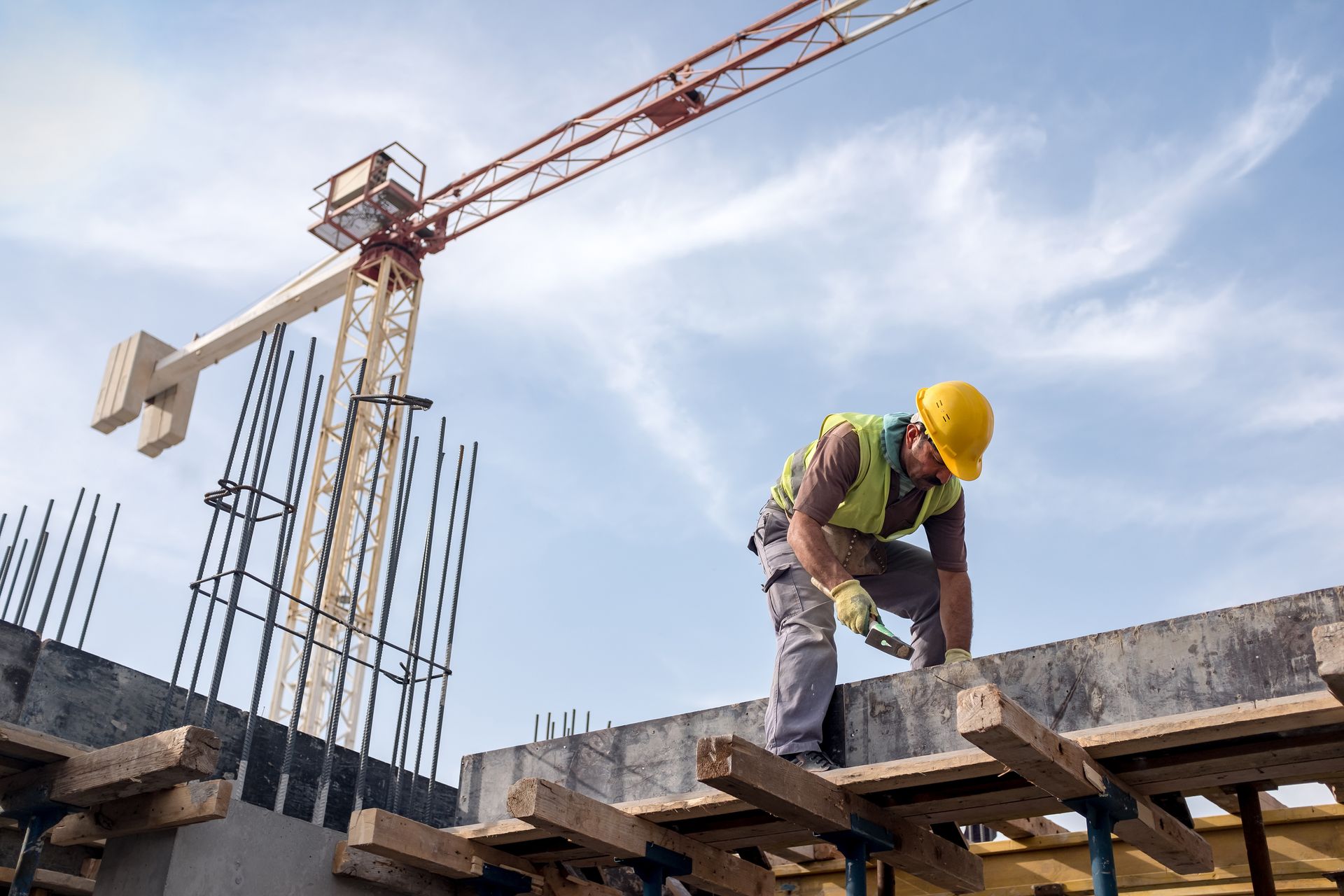