OSHA REQUIREMENTS FOR SMALL BUSINESSES – WHAT YOU NEED TO KNOW
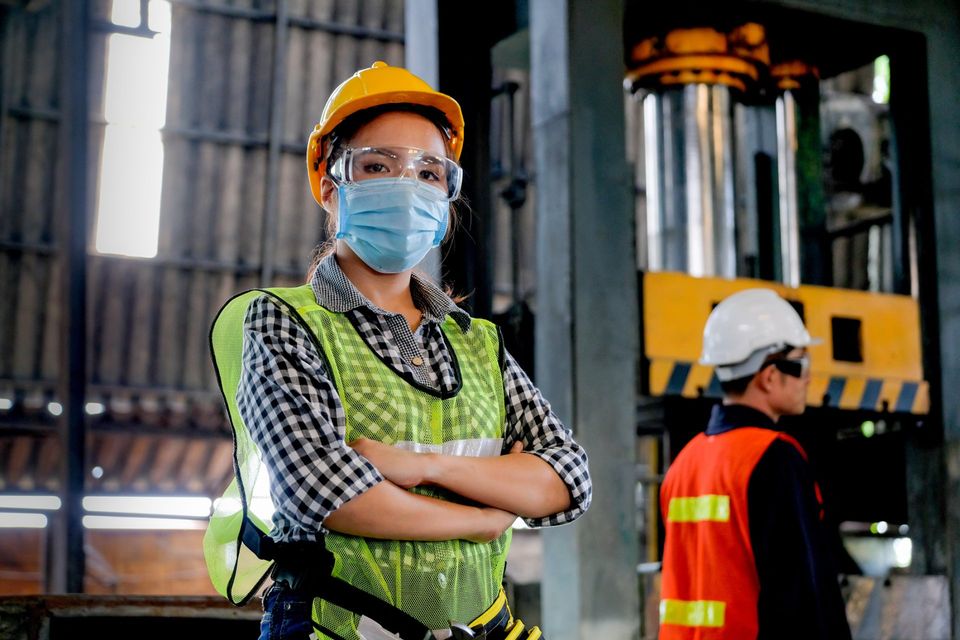
The Occupational Safety & Health Administration (OSHA) is a division of the United States Department of Labor. OSHA was created in 1971 to administer the Occupational Safety and Health Act of 1970. The act established a nationwide program to protect workers from injury, illness, and death caused by unsafe working conditions. Small businesses are required to comply with OSHA regulations.
Abiding by OSHA laws is not only required, it makes smart business sense. Employees who become ill or are injured due to unsafe working conditions are costly. Reductions in staff morale, decreased productivity, significant costs, and high turnover are often direct results of inadequate attention to the quality of the workplace.
Getting Started
OSHA and small businesses share the responsibility when it comes to fostering a healthy and safe place in which to work. It is essential that you become knowledgeable about the specific OSHA regulations that apply to your business. Not knowing may result in worker injury, hefty fines, and severe penalties. Due to the diversity of small business fields, the complexities of OSHA requirements, and the potential fines and penalties for non-compliance, you may be asking yourself, “Where do I start?”
Enrollment in industry-specific OSHA training classes is a cost-effective, proven method of learning about what is required. The right training program begins with an assessment of your business. The finest OSHA training classes give business owners, managers and staff the tools to work within in the law and improve their respective working conditions.
SEA Inc. is a leader in OSHA compliance education. With emphasis on customized training, SEA Inc. offers powerful compliance programs that go beyond teaching regulations. Conducted in a classroom environment, either on-site or at a training facility, knowledgeable and experienced instructors guide students through a hands-on experience that meets or exceeds OSHA requirements.
Planning and Training for the Proposed Changes
Although EPA is already planning webinars to help bring NPDES organizations up to speed with the new rule, the experts at SET believe that hands-on training offers a far better option for those NPDES-permitted municipalities, businesses and industries that must make changes to meet the new reporting requirements. That is why SET offers comprehensive training, planning and consulting, not only for NPDES compliance but for such programs as Hazardous Waste Management, RCRA Compliance, DOT, SPCC, and Hazardous Materials Management as well. SET training instructors have updated industry knowledge and the ability to convey that information in an understandable format to managers and workers who deal with the handling and disposal of hazardous materials or industrial waste.
OSHA 10 Training
OSHA 10 training from SEA Inc. is a one-of-a-kind program, designed to take students step-by-step through OSHA regulations tailored to their business needs. The OSHA Ten Hour training course covers all aspects of navigating through the often-confusing ocean of OSHA requirements. Business leaders learn to protect employees, fill out reports, and communicate with OSHA representatives. In addition, they learn about the most common industry fines and violations and how to avoid them.
The OSHA Ten Hour training course assists business professionals in engaging each employee in the safety compliance process. Involved employees are more likely to work within the rules and avoid mistakes.
SEA Inc. also offers a more comprehensive 30-hour training class, designed to delve even further into the intricacies of working within OSHA regulations.
Avoid Fines and Penalties – Enroll Today
SEA Inc. is comprised of a fully accredited team with over 225 years of combined safety, health, and compliance expertise. Ongoing training and continuing education ensures that instructors stay current about the latest additions and changes to OSHA regulations. Each course is presented in an appealing way that encourages learning and knowledge retention.
SEA Inc. offers affordable OSHA training options designed exclusively for your business. Tailored to your individual needs, SEA Inc. programs provide the detailed instruction and hands-on training that keep you OSHA compliant and increase worker health and safety.
Enrolling is easy. Contact us or call 501-568-3111 or toll free 888-627-8740 to learn how.
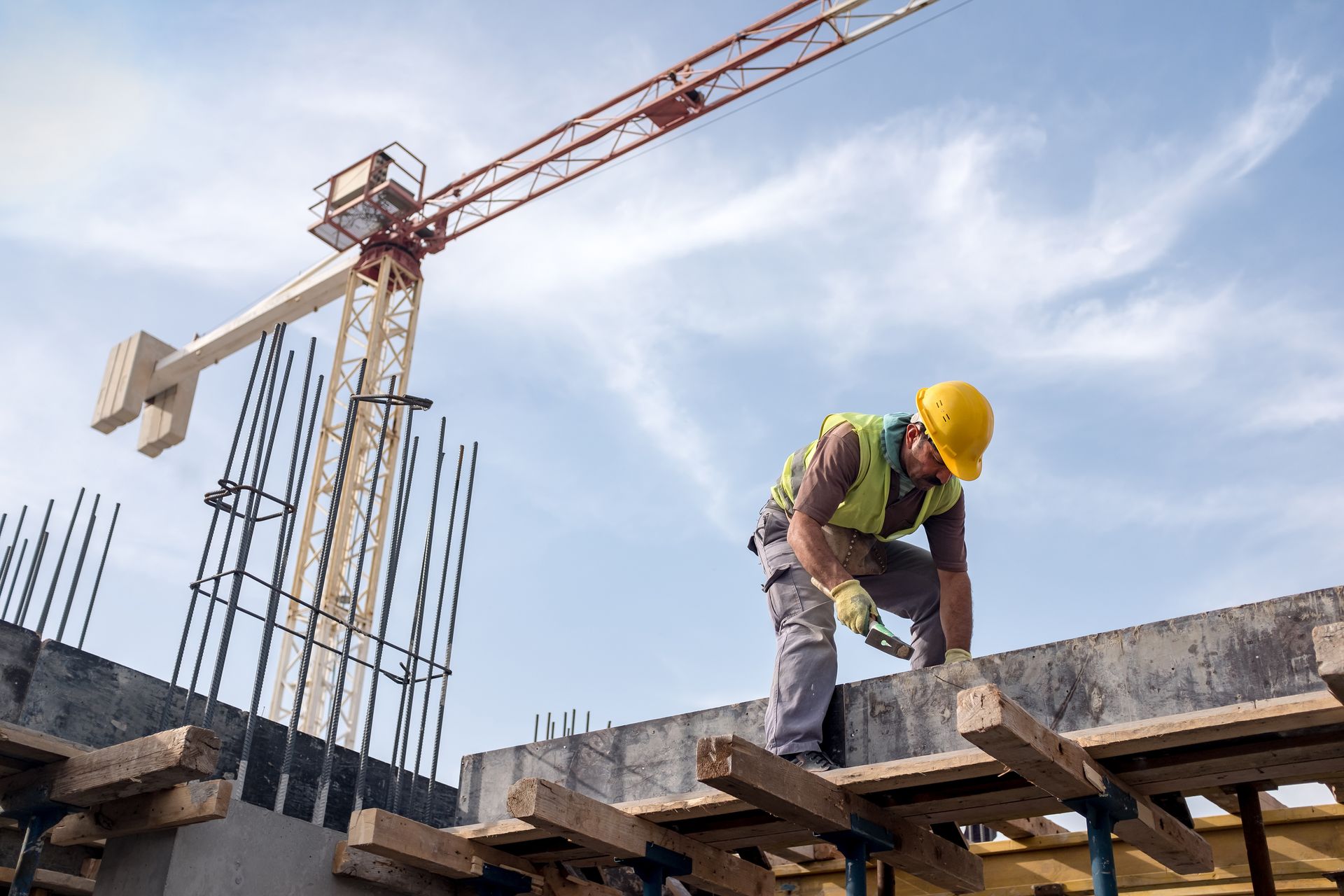
Each year, as the Occupational Safety and Health Administration (OSHA) releases its list of the top 10 workplace safety violations, a pattern emerges that begs a question: Are these frequent violations a sign that employers continue to struggle with the same safety issues, or does it reflect a disposition among OSHA inspectors to focus on areas where they are trained to focus? The Persistent Issue of Repeated Findings The repetition of certain violations year after year might seem surprising, but it underscores a significant challenge in workplace safety management. The top violations tend to be those that are most visible and easiest to spot during inspections, such as fall protection and hazard communication. This consistency suggests that while awareness is high, practical implementation and adherence to safety practices lag behind. Top 10 Most Cited Health and Safety Standards of 2024 1. . Fall Protection, General Requirements: 6,307 violations For the 14th consecutive year, fall protection tops the list of OSHA's enforcement priorities. This emphasis is not arbitrary; OSHA has designated fall protection as a national emphasis area, making it a primary focus during inspections. It's often one of the easiest violations to spot without extensive investigation skills. The OSHA standard 1926.501 mandates that employers must provide fall protection systems like guardrails, safety nets, or personal fall arrest systems for workers at risk of falls of six feet or more in construction and four feet in general industry. Often, the major factor in these violations is human behavior. Many offenders might think, "No one is watching, and this will only take a moment, so it's no big deal." However, this mindset can lead to non-compliance with critical safety measures, putting worker safety at significant risk.